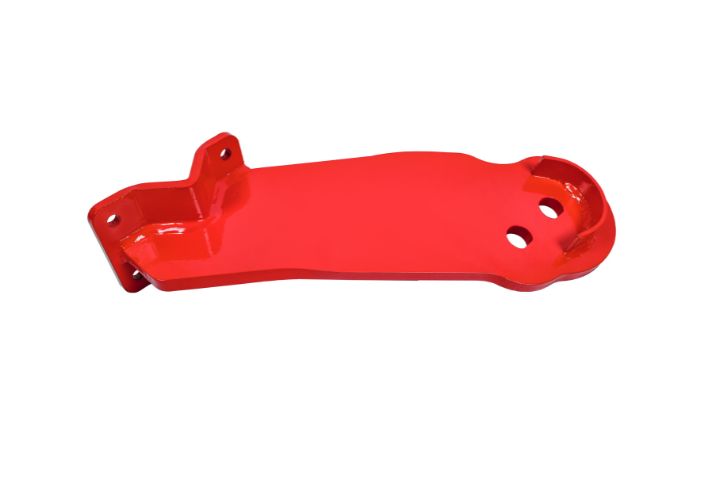
Hindustan Pressings Private Limited – Sheet Metal Components Manufacturer
Powering Material Handling Performance with Precision Sheet Metal Components
At HPPL India, we’re not just experts in metal sheet components; we’re your partners in advancing agriculture. We understand the intricate balance of strength, precision, and efficiency that defines your agricultural equipment. That’s why every metal sheet component we create is designed to embody agricultural excellence.
But HPPL India is more than just a manufacturer; it’s about teamwork. We’re your trusted collaborators, working closely with you from the initial idea to the final production phase. Our team of skilled engineers and technicians are here to help bring your agricultural vision to life, paying close attention to every detail.
HPPL India is your one-stop destination for all your agricultural sheet metal needs. We offer a wide range of services, including laser cutting, CNC bending, welding, and surface finishing. We’re here to solve your complex design challenges, provide a reliable source for large-scale production, and be your agile partner for quick prototyping.
So, let HPPL India be the driving force behind your agricultural goals. We’re the foundation of your machinery, the strength that fuels your productivity, and the trusted partner who guides you from concept to success. Get in touch with us today and experience the HPPL India difference in shaping the future of agriculture.
Ready to enhance your operations with precision-engineered sheet metal components?
Our team at HPPL is here to provide tailored solutions to meet your industry’s needs.
At HPPL India, we use lasers and presses to expertly shape steel into the intricate sheet metal components that are essential for various agriculture equipment, including Tillage & Cultivation Equipments, Planting & Seeding Equipments, Harvesting & Processing Components. Our precision and dedication in crafting components that form the foundation of agricultural excellence.
At HPPL, we specialize in providing precision sheet metal components for the material handling industry, ensuring the strength, reliability, and functionality of your equipment. From conveyors to hoists and cranes, every part we manufacture is designed to optimize performance, reduce downtime, and improve the efficiency of your material handling systems. Our advanced technology and expert craftsmanship deliver components that meet the demanding standards of modern industry.
Stamping is a manufacturing process used to shape metal sheets into specific designs through the application of pressure. The process involves placing a flat metal sheet, known as a blank, into a stamping press, where it is shaped by a die. The die and press work together to cut, bend, or form the metal into the desired shape, producing parts with precise dimensions. Stamping is commonly used in industries such as automotive, aerospace, and electronics to produce components like panels, brackets, and connectors, offering high-speed production and consistent quality for mass manufacturing.
Our laser cutting technology provides the precision and flexibility needed for material handling applications. By using high-powered lasers, we can cut, shape, and engrave metal sheets with high accuracy, producing components like brackets, housings, and structural parts. This process minimizes material waste while ensuring clean, intricate cuts that meet the exact specifications required for efficient material handling.
Precision is critical in material handling equipment, and our CNC bending capabilities ensure complex parts are shaped to perfection. By leveraging CNC technology, we achieve precise, repeatable bends that are crucial for parts such as frames, brackets, and custom enclosures. Our CNC bending process ensures that each part fits seamlessly into your material handling systems, providing consistent performance.
HPPL’s MIG and TIG welding processes offer strong, precise joints for material handling components. MIG welding is ideal for quickly joining thicker materials, while TIG welding allows for greater control and precision for thinner metals. These welding techniques ensure durable, high-quality welds that are essential for parts exposed to heavy loads and repetitive stress in material handling equipment.
Accuracy and quality control are paramount in the material handling industry, and our CMM ensures every part meets the required specifications. Using advanced measurement technology, we meticulously inspect each component’s dimensions, geometry, and alignment to guarantee that your material handling systems operate efficiently and reliably.
To meet high-volume production demands in the material handling industry, HPPL employs robotic welding to ensure consistency, speed, and precision. Robotic welding enhances productivity while maintaining top-quality welds, ideal for large-scale manufacturing of material handling equipment components that require durability and strength.
HPPL’s tooling expertise is at the heart of our ability to create highly accurate components for material handling systems. With custom-designed dies, molds, and fixtures, we ensure that each metal part is precisely formed, cut, and assembled. Our tooling ensures consistency and efficiency, driving productivity in the manufacturing of components such as conveyors, lifts, and other material handling solutions.
Quality/accuracy accepted in the industry
Machine/Plant capacity considered in industry.
How HPPL is more time efficient.
How HPPL is cost-efficient
HPPL stands as a trusted partner for the material handling industry, offering precision-engineered sheet metal components that enhance performance, reliability, and longevity. Our expertise, combined with cutting-edge technology, ensures that each part meets the stringent demands of the material handling sector, from production efficiency to system durability. Choose HPPL to power your material handling solutions with high-quality, cost-effective components.
We utilize a wide range of high-grade sheet metals to suit diverse agricultural needs, including mild steel, stainless steel, aluminum, and galvanized steel.
Absolutely! We excel in collaborating with clients to design and manufacture custom components that perfectly match their unique requirements and equipment specifications.
.
We adhere to strict quality control standards throughout the entire manufacturing process, utilizing advanced techniques like CMM inspections to ensure every component meets your exact specifications and delivers optimal performance.
Our turnaround times vary depending on the complexity of the order and your specific needs. We strive to provide competitive lead times while maintaining the highest quality standards.
Yes, we are committed to sustainability and utilize eco-friendly practices whenever possible, including minimizing waste, recycling materials, and using energy-efficient technologies.
We utilize different welding processes like MIG, TIG, and spot welding, depending on the material, thickness, and desired strength of the joint.
We offer several competitive advantages, including:
- Extensive experience in the agriculture industry
- High-quality materials and workmanship
- Competitive pricing
- Fast lead times
- Customizable solutions
- Excellent customer service
Visionaries Redefining Agricultural Frontiers