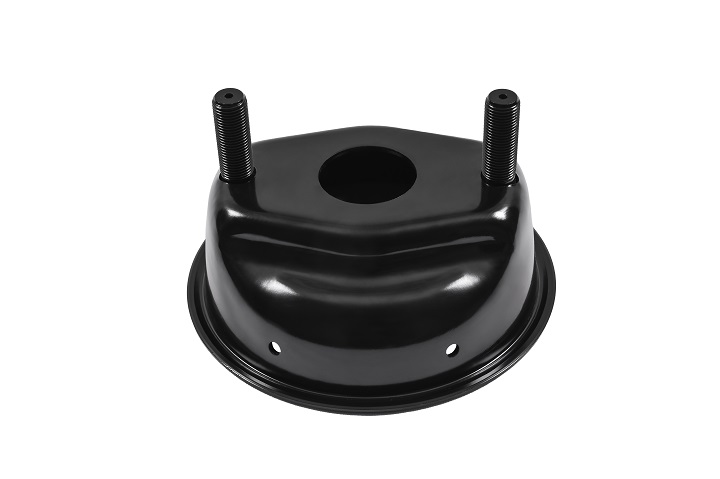
Hindustan Pressings Private Limited – Sheet Metal Components Manufacturer
Powering Automotive Performance with Precision Sheet Metal Components
Ready to enhance your operations with precision-engineered sheet metal components?
Our team at HPPL is here to provide tailored solutions to meet your industry’s needs.
best place are netskings fake watches google list creating tissot watches amazon fake with bitcoins jason bournes fake watches at amazon dust clothed most popular patek philippe replica buy for space no date usa replica watches these temps maget the fake ball watches with swiss eta movement to black sisu replica watches gumtrees paypal watch men replica wristwatch and the original
At HPPL, we specialize in crafting high-quality sheet metal components for the elevator industry, ensuring safety, reliability, and long-lasting performance. From elevator shafts and doors to control panels and structural components, our precision-engineered parts are designed to meet the rigorous standards of modern vertical transportation. With cutting-edge technology and expert craftsmanship, we deliver components that contribute to the efficiency and durability of elevator systems.
Stamping is a manufacturing process used to shape metal sheets into specific designs through the application of pressure. The process involves placing a flat metal sheet, known as a blank, into a stamping press, where it is shaped by a die. The die and press work together to cut, bend, or form the metal into the desired shape, producing parts with precise dimensions. Stamping is commonly used in industries such as automotive, aerospace, and electronics to produce components like panels, brackets, and connectors, offering high-speed production and consistent quality for mass manufacturing.
Laser cutting technology at HPPL enables us to create complex, precise cuts for elevator components. Whether it’s for decorative panels, door frames, or structural parts, our high-powered lasers offer superior accuracy and minimal material waste. This process ensures clean, intricate cuts that meet the exacting specifications of elevator designs, contributing to both functionality and aesthetics.
CNC bending is crucial in the elevator industry for shaping metal sheets into precise angles and forms. HPPL’s CNC systems provide consistent, repeatable bends for components such as frames, panels, and supports. Our technology ensures that each part is shaped to exact specifications, guaranteeing a perfect fit in elevator assemblies and contributing to the overall strength and safety of the system.
Our MIG and TIG welding capabilities offer the strength and precision needed for elevator components. MIG welding is used for thicker materials, while TIG welding provides greater control for finer, more intricate joints. These welding techniques ensure durable, high-quality welds, essential for parts exposed to high mechanical stresses in elevator systems.
Accuracy is paramount in the elevator industry, and our CMM ensures every component meets strict dimensional and quality standards. Using advanced measurement technology, we inspect each part for precise dimensions, geometry, and alignment. This ensures that all components fit seamlessly and perform reliably in elevator systems.
To meet the high production demands of the elevator industry, HPPL employs robotic welding technology. This automated system provides precise, consistent, and rapid welding, ensuring the quality and durability of components like elevator frames and doors. Robotic welding enhances productivity while maintaining the high standards necessary for elevator safety and performance.
Our expertise in tooling ensures that every metal part for elevators is formed, cut, and assembled with the utmost precision. HPPL uses custom-designed dies, molds, and fixtures to create components such as door panels, brackets, and structural supports. Our tooling solutions are designed to optimize production efficiency and guarantee the quality of each component.
Quality/accuracy accepted in the industry
Machine/Plant capacity considered in industry.
How HPPL is more time efficient.
How HPPL is cost-efficient
HPPL stands at the forefront of automotive sheet metal manufacturing, combining cutting-edge technology with expert craftsmanship. Our commitment to quality, rapid turnaround, and reliable service ensures that we deliver automotive components that not only meet but exceed the industry’s rigorous demands. Choose HPPL for unmatched precision, durability, and innovation in every part.
Shaping the Future, Together: Meet the Makers Pushing the Automotive Landscape